The debate on whether a better instrument can be made by hand or by machine is not likely to go away anytime soon. A CNC (computer numerically controlled) router is essentially a cutting tool fed pathway information by a design program. The CNC process excels at accuracy, repetition and safety but has a reputation of producing “cookie cutter” designs. On the other-hand, building a guitar with “hand tools” has a connotation of a seasoned craftsmen using nothing but chisels and their sharp wit but, is prone to being time consuming and costly. In my opinion, both have been tainted by marketing teams. A good CNC technician needs just as much knowledge as the seasoned luthier. Likewise, the handcrafting builder likely uses a wide number of power tools to speed up their process.
I prefer to use the best tool for the job. In some places that’s my CNC and in others that’s a 20 year old card scraper I found at a garage sale. As every instrument is different from the last so too is my usage of CNC/hand tools.
About Vigilant
My shop is located in James Bay, a suburb of Victoria, British Columbia, Canada. Vigilant was founded in 2015 and has quickly grown into business where I specialize in working with extended range guitars, multi scale instruments, exotic woods and environmentally conscious products. I want my instruments to be as unique as the musicians who play them so I’m always happy to try new technologies, products and processes to make your dream guitar!
I take great pride in building guitars from scratch and giving customers a uniquely Canadian instrument. I want like-minded entrepreneurs to thrive which is why I make a point to purchase products made in Canada before looking elsewhere. This may be a paint, a pickup, a guitar strap, a tool or a bridge; any component or accessory to the guitar industry is fair game. While this may increase the cost of our instruments I would rather support the Canadian economy through ingenuity, hard work and product development rather than follow other builders in a race to the bottom to get the cheapest product at the cheapest price. Cheap has a bad sound and I don’t like making bad sounding guitars.
My Process
What makes Vigilant, Vigilant?
CNC vs Handmade
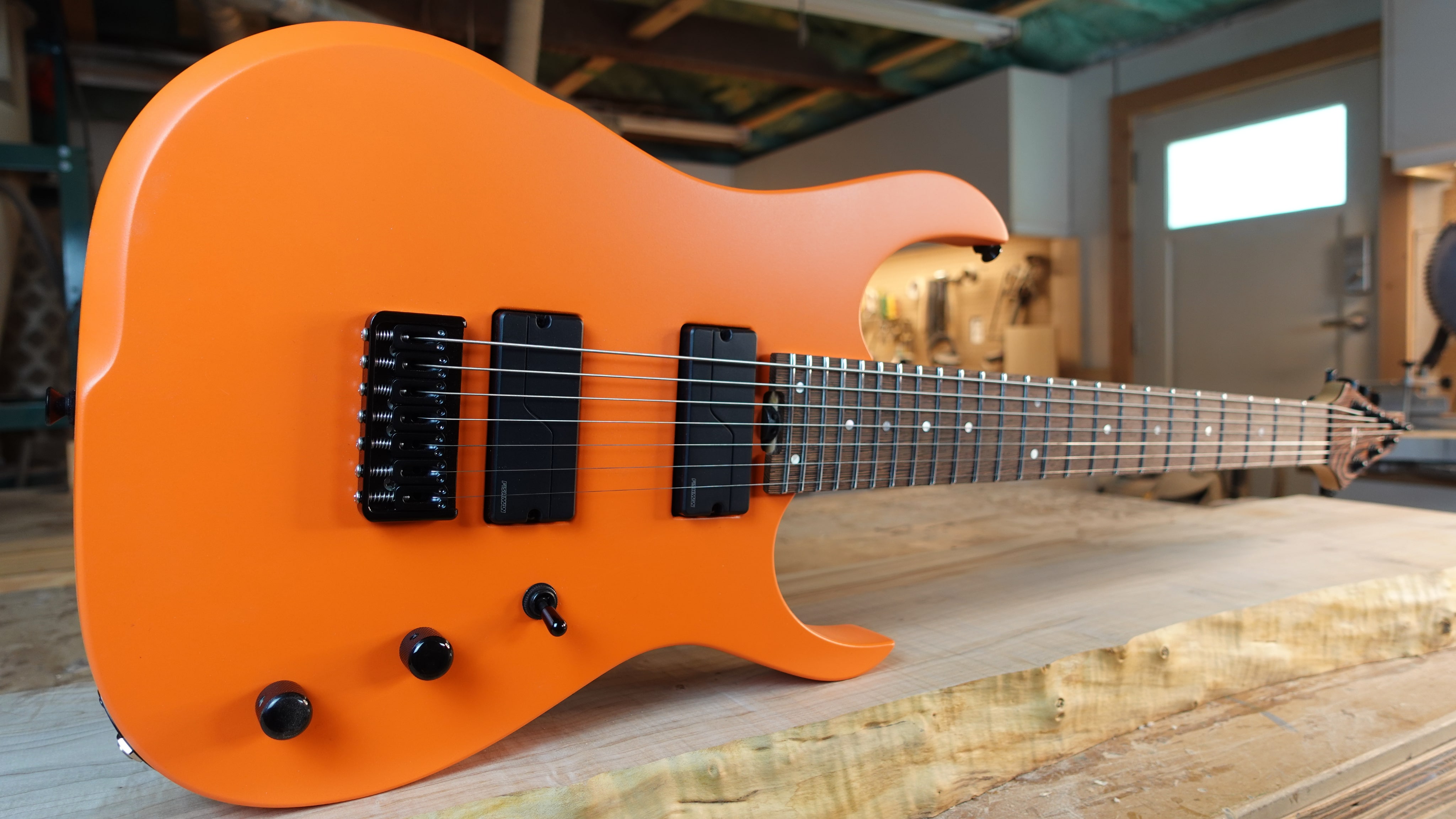
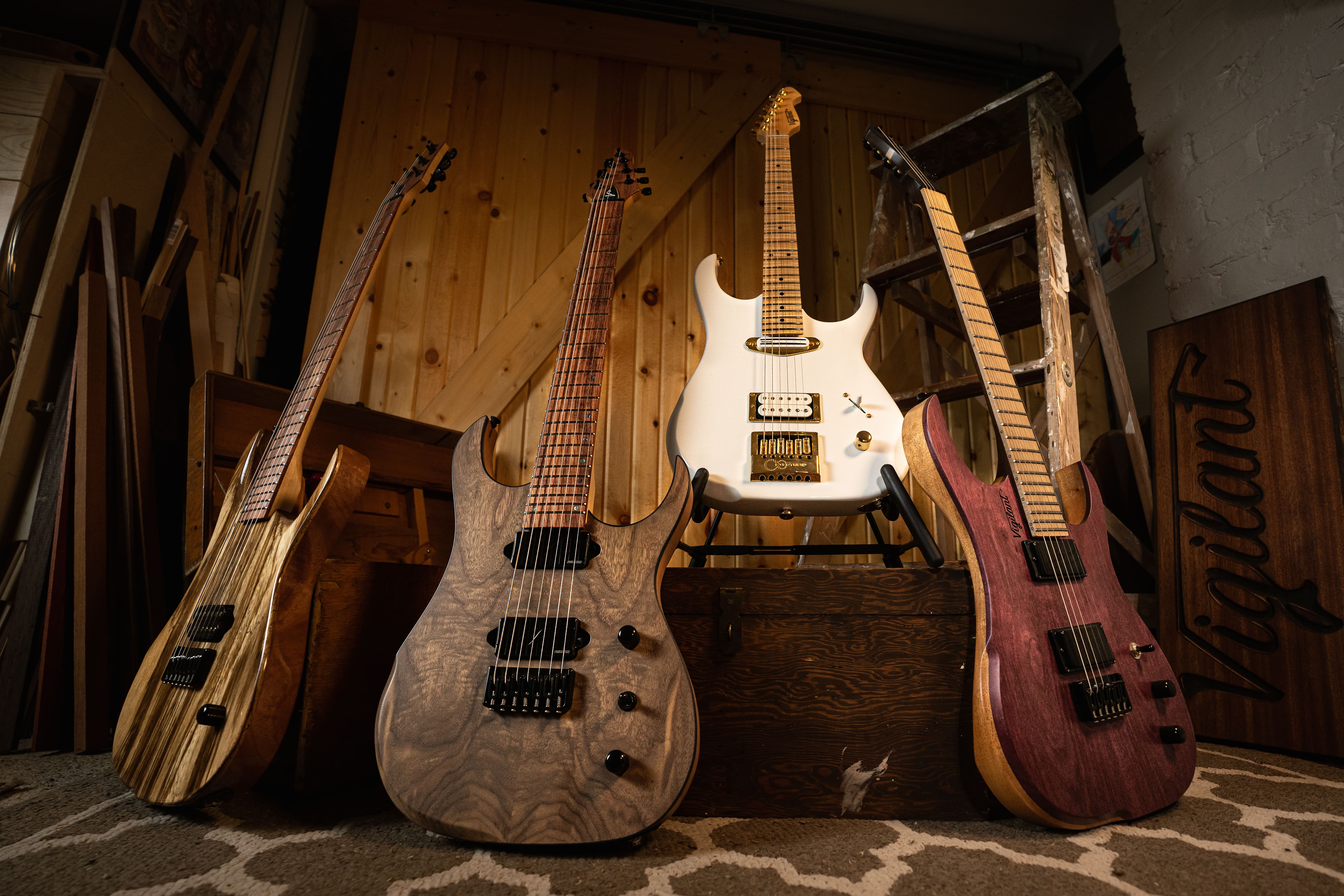
Where I use CNC:
In most cases, a bulk of the electronic cavity routing, inlays, fret slotting and shaping is done on the CNC. This guarantees a safe, cost effective and accurate process that leaves me mentally and physically charged to focus on more detail oriented matters. The CNC also allows me to create customized templates and jigs that can accelerate an otherwise time consuming hand tool process.
Where I use hand tools:
I prefer to use hand tools in situations where the margin for error is quite high or where a task requires a healthy degree of trepidation. I carve my necks with hand/power tools and do all of the final fretwork, sanding and finishing with rudimentary scrapers, chisels, gouges and blades. In many cases, they are safer, less noisy and offer a degree of adaptability that current CNC technology can’t match.
Building Duration
Production builds with standardized specs will take between 8-10 weeks because I have all the jigs, measurements and tools ready to go. Most custom builds will take between 3-5 months depending on waitlists, the seasons and the intricacy of the project. Much of this time is consumed by three processes:
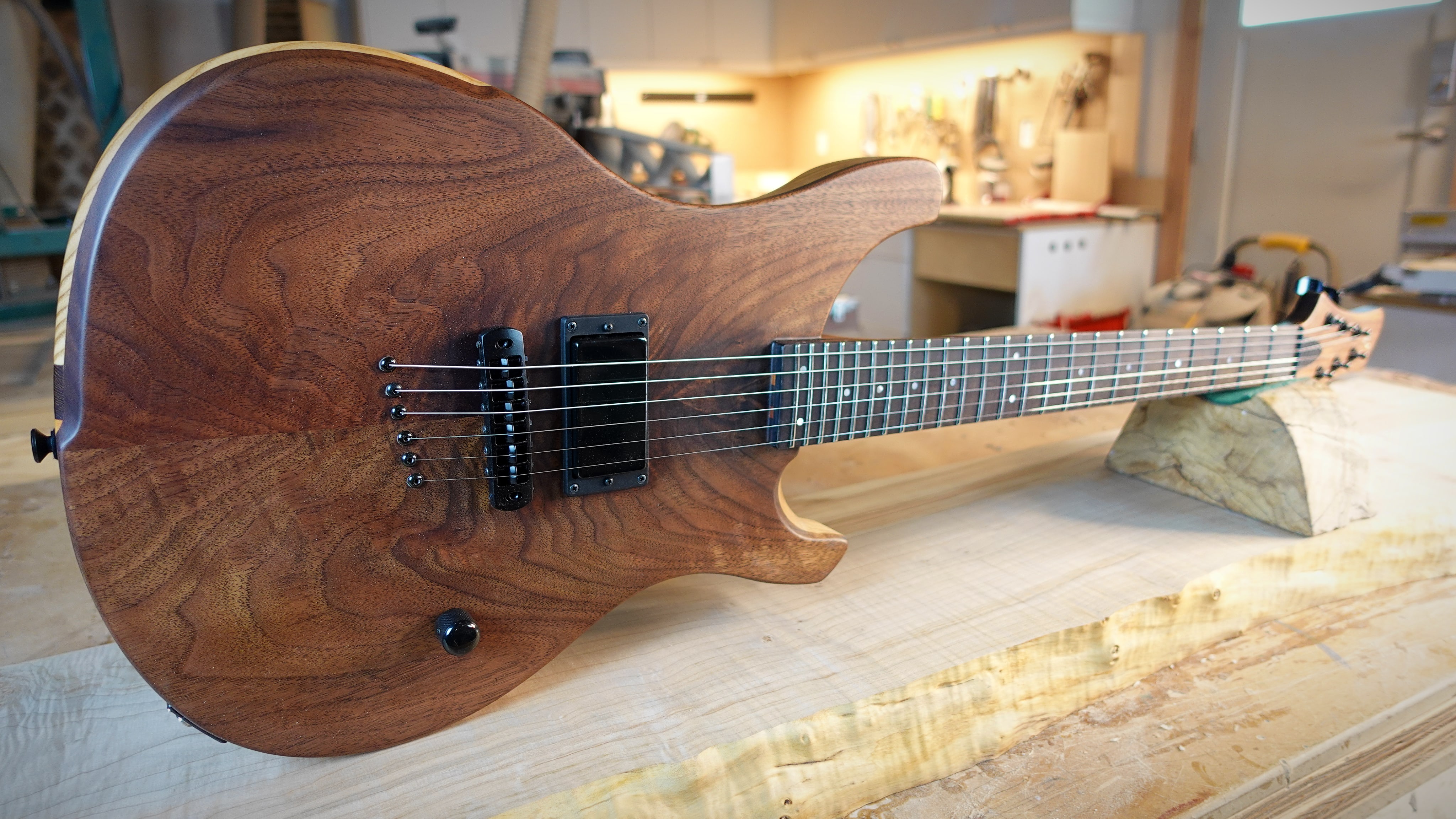
- Collecting the electronics, hardware, timber and products from multiple suppliers.
- Allowing the timber to settle between working ie. letting the neck settle after carving the profile to ensure it stays straight.
- Giving the finish enough time to cure before polishing.
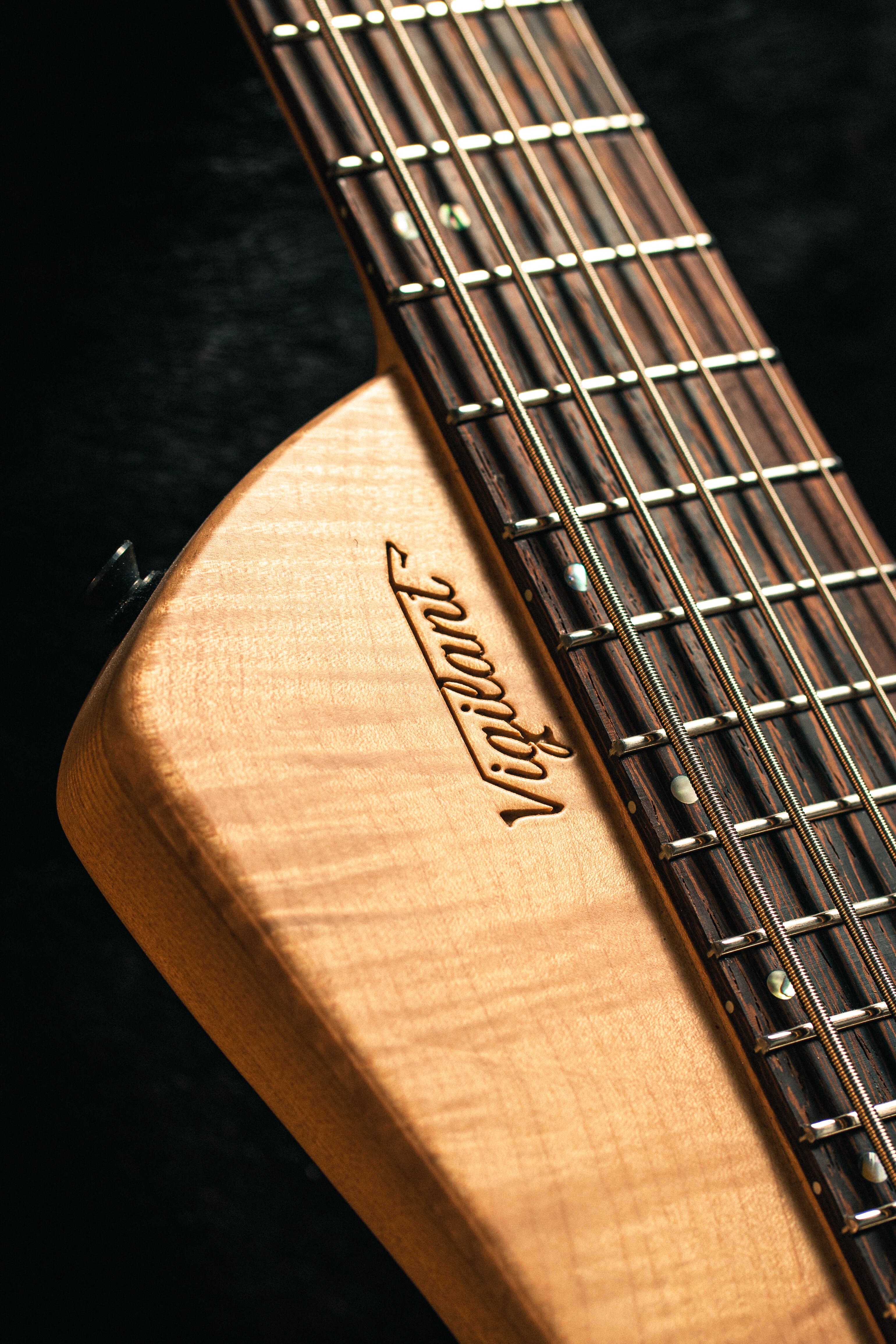
Environmental Considerations
Building guitars, like any building process, creates a degree of waste. There are wood offcuts, sawdust, consumables and products that are required to complete the project which cannot be recycled or reused. While I won’t sacrifice the quality of a project’s outcome based on how much waste it creates, I will pursue the use of products that are environmentally sustainable to mitigate the amount of waste I create.
This sustainability may come in several iterations in any given project:
2018
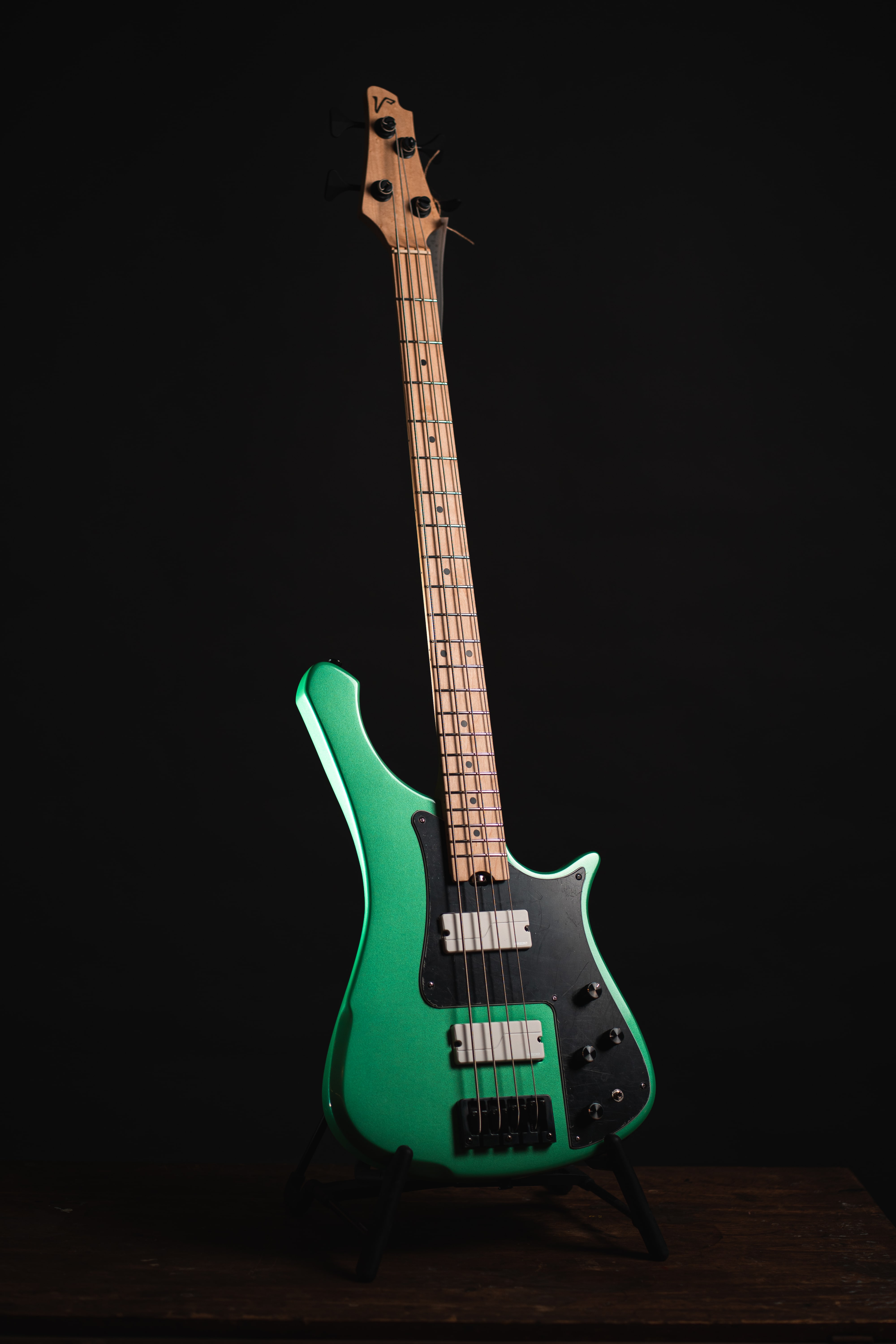
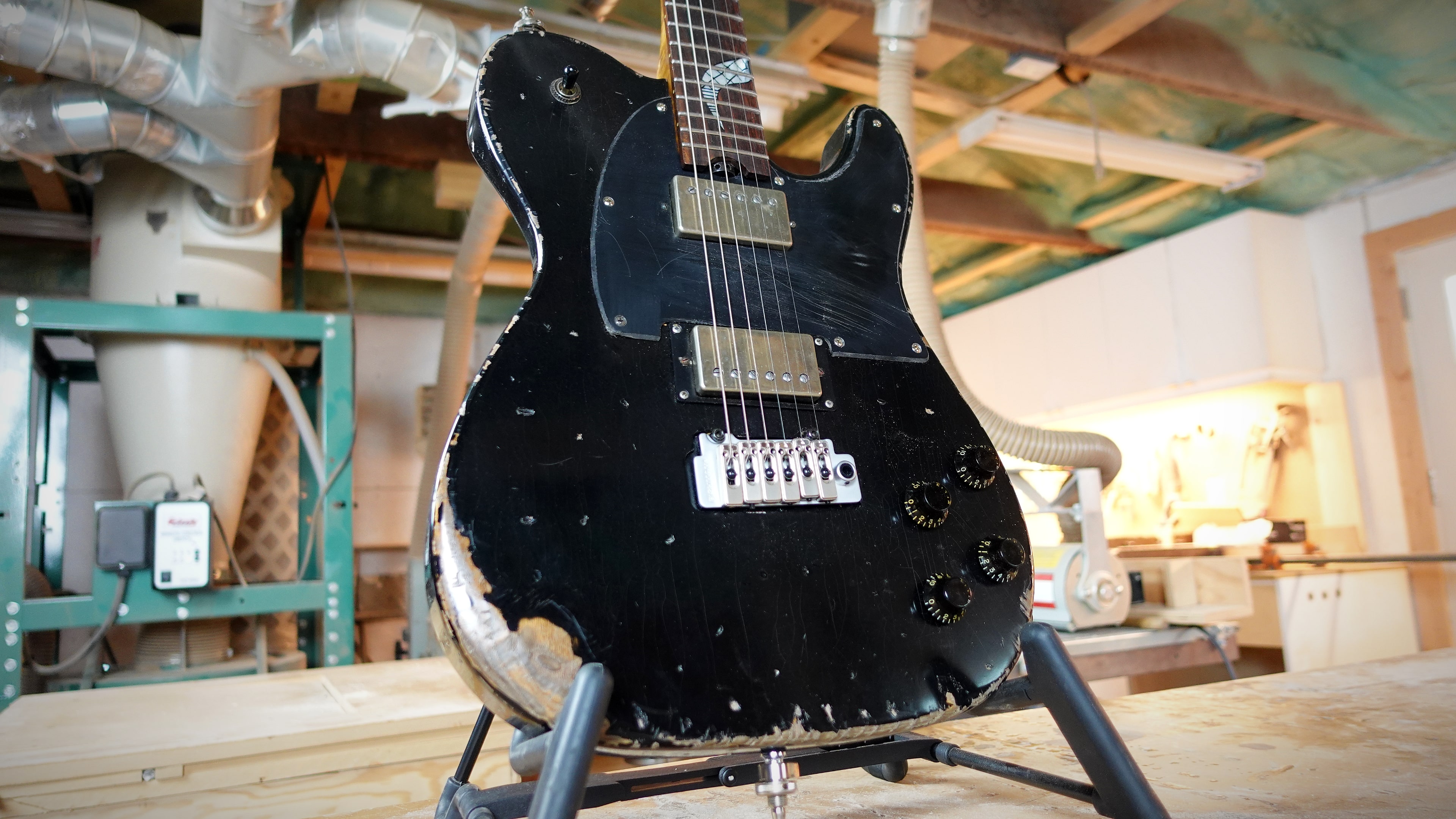
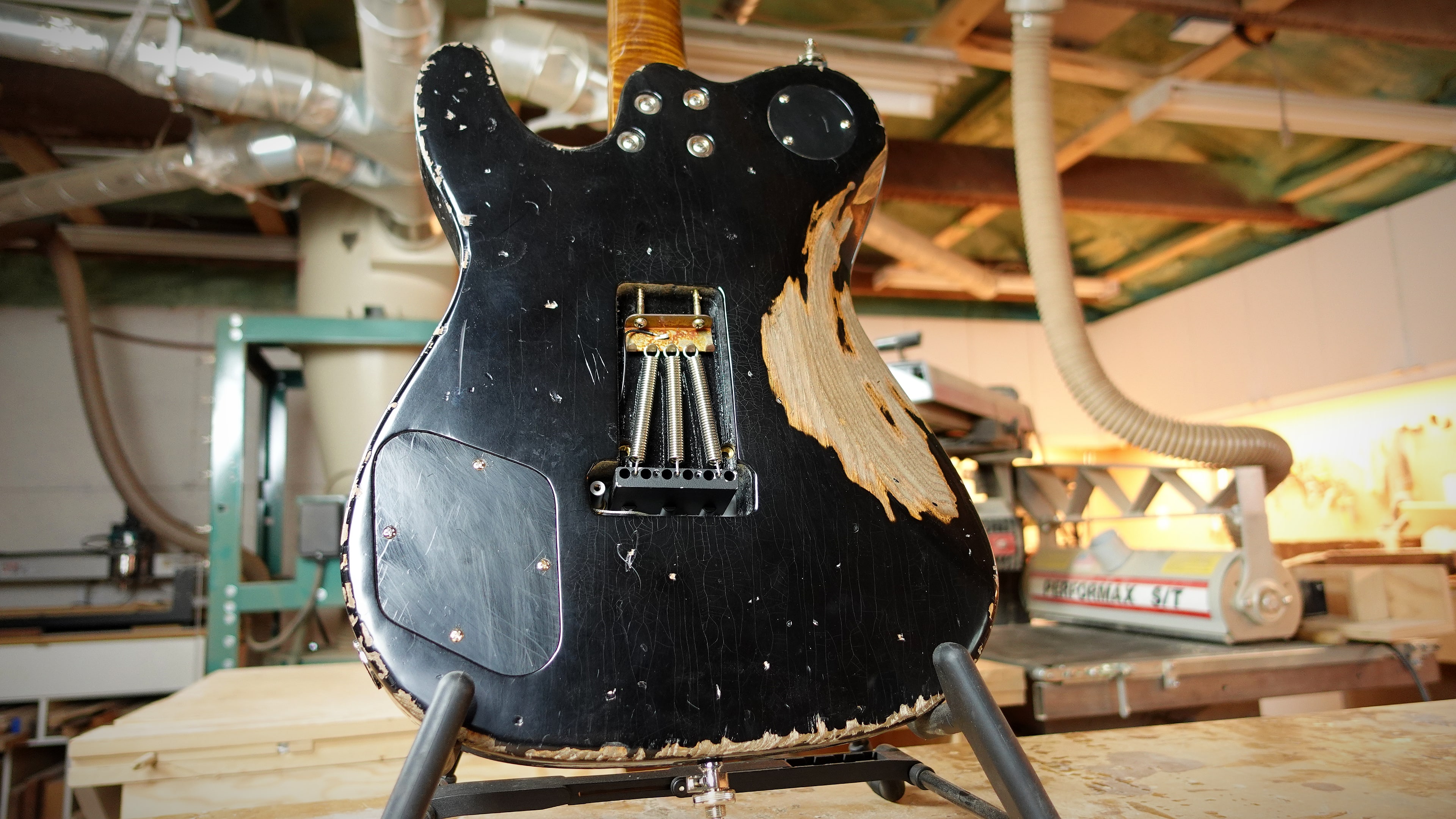
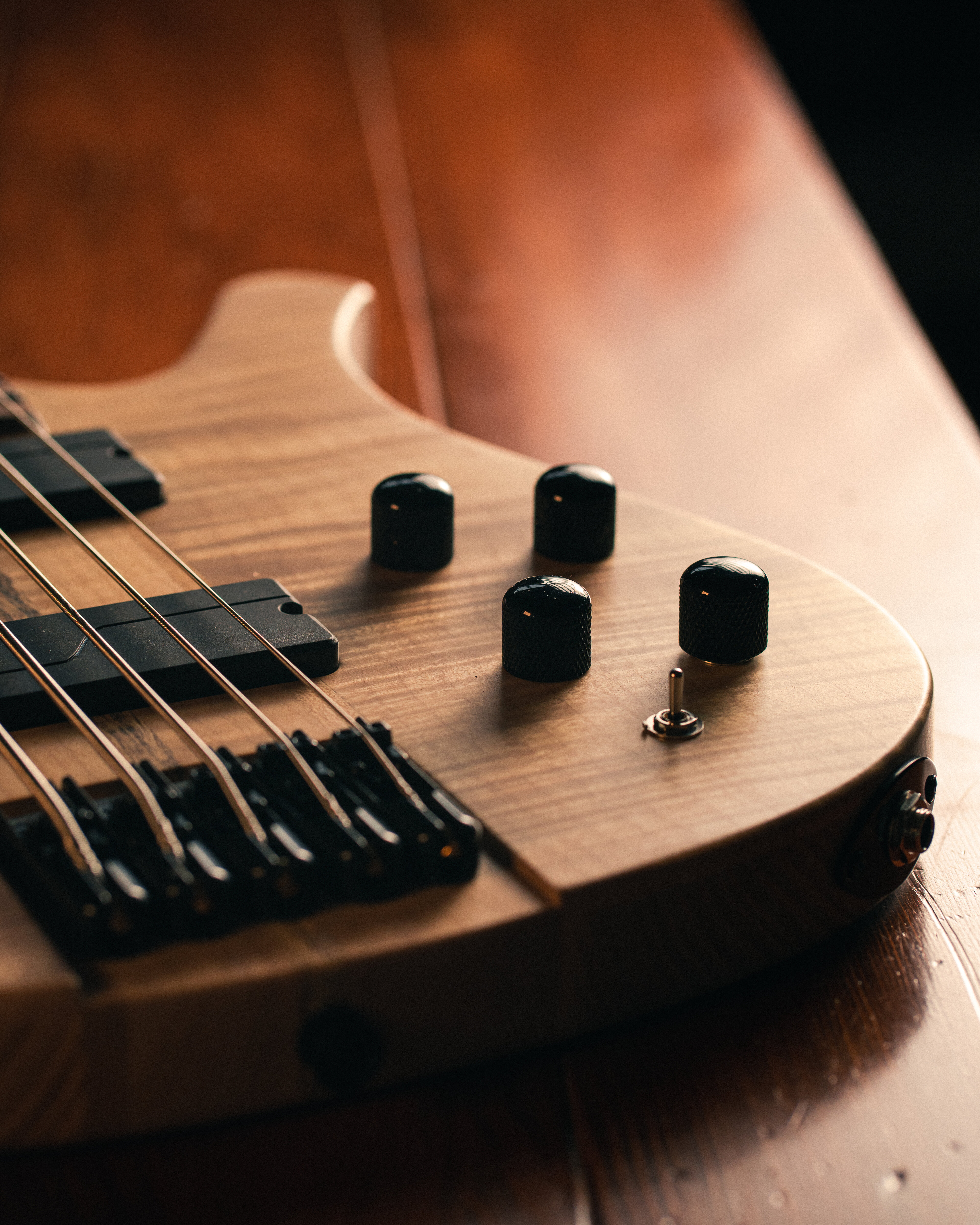
The wood
I will strive to use ethically, legally and sustainably harvested wood from reputable dealers. Where possible I will make an effort to reduce the length of supply chains by sourcing wood from the Pacific Northwest thus reducing shipping emissions. I will also strive to use sustainable alternate timber materials not typically found in production instruments ie. softwoods, synthetic fingerboards, hempwood, richlite etc… Indeed many of these alterations will affect the sounds and look of the instrument but I want my instruments to look and sound sustainable.
The hardware
If one were to look at how much energy goes into making a simple screw they may be surprised. The dirt needs to be mined, then smelted and cast into an ingot, shaped, plated, packaged, shipped and sold to a retailer where it is then re-packed, shipped and sold again to purchasers like myself. While that 1 screw may only cost 10 cents to buy how much gas do you think it burned just getting to my shop?
To combat this process I prefer to use hardware from companies that strive to offset their emissions or use products that use sustainable materials. Using local machinists to make bridges, locally manufactured pickups or reputable companies like Graph Tech for their Tusq nuts and tuners is a step in the right direction to not only cut down on the waste but to also achieve a uniquely West Coast sound!
The Finishing Products
The guitar industry has a long reputation of using highly volatile organic compounds (VOCs) in the stains, primers, paints and clear coats that protect our projects. The manufacturing processes that create historically used finishes like nitro-cellulose lacquer, polyurethanes, epoxies and flaked paints takes a toll not only on the planet but on the health and safety of the finishing technicians. I believe that water based finishing technology has reached the point where it can compete with traditional stains, paints and lacquers. The use of water finishes greatly reduces VOCs giving consumers an ease of knowing that when they buy a Vigilant guitar they are part of the global environmental solution.